-
Car Parts Mold
-
Plastic Auto Parts Mould
-
Automotive Injection Mold
-
Double Shot Injection Molding
-
Medical Injection Molding
-
Multi Cavity Injection Molding
-
Electronics Injection Molding
-
High Temperature Plastic Mold
-
Unscrewing Mold
-
Home Appliance Mould
-
Gear Mold
-
Overmolding Injection Molding
-
Plastic Mold Components
-
StefanWe are pleased to have cooperated with ERBIWA, and thanks for your supports to our each project.
-
RobertIt's very nice to receive the molds with hig quality and superior service, but favourable price. We will continue to cooperate with you in future projects.
-
CarlosYou are a dynamic and powerful team, i have seen the future of Chinese manufacturing from you all.
ERBIWA Mould - Medical Grade High Precision P20 Steel Disposable Plastic Syringe Injection Mould (Sterile Packaging Comp
Place of Origin | Guangdong, China |
---|---|
Brand Name | Erbiwa Mould |
Certification | ISO 9001: 2015 IATF 16949: 2016 |
Model Number | Customized |
Minimum Order Quantity | 1 Set |
Price | negotiation |
Packaging Details | Standard export package |
Delivery Time | 30-60 Days |
Payment Terms | TT, L/C, D/A, D/P, T/T, Western Union, MoneyGram |
Supply Ability | 1 set per month |
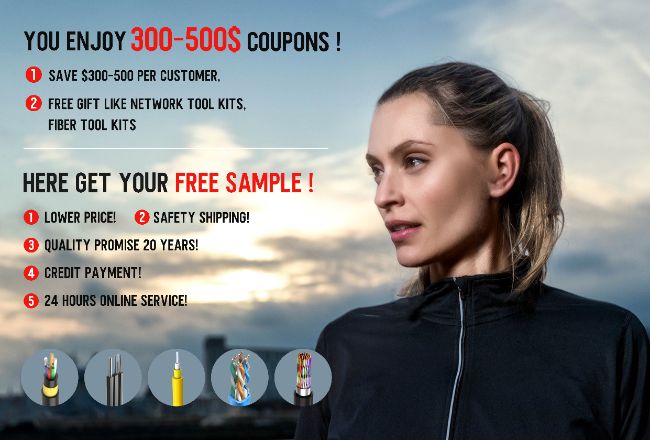
Contact me for free samples and coupons.
Whatsapp:0086 18588475571
Wechat: 0086 18588475571
Skype: sales10@aixton.com
If you have any concern, we provide 24-hour online help.
xFeatures | Attractive And Durable | Quality Control | Inspected And Reconfirmed Before Shipment |
---|---|---|---|
Mold Runner | Cold Runner And Hot Runner | Plastic Production Raw Material | PP, PA6, PLA, ABS, PE, PC, POM, PVC, PET, PS, TPE/TPR, Etc |
Product Name | Professional-Grade Car Parts Mold For Superior Automotive Components | Month Production | 50 Sets Per Month |
Highlight | Disposable Plastic Syringe Injection Mould |
ERBIWA Mould - Medical Grade High Precision P20 Steel Disposable Plastic Syringe Injection Mould (Sterile Packaging Compatible)
Technical Parameters:
Technical Parameter | Value |
---|---|
Mold Runner | Cold Runner And Hot Runner |
Quality Control | Inspected And Reconfirmed Before Shipment |
Product Category | Car Parts Mold |
Month Production | 50 Sets Per Month |
Size Tolerance | +/-0.05mm |
Steel Material | 718H, P20, NAK80, S316H, SKD61, etc |
Features | Attractive And Durable |
Mould Price | Cost-Effective And Competitive |
After-Sales Service | 12 Months For Free |
Delivery Time | 30-60 Days |
This Car Parts Mold product is perfect for quality automotive parts, custom car parts, and automotive parts manufacturing.
Product Features
Medical-grade material: Adopting high-quality P20 steel with high hardness and corrosion resistance to ensure the long-term stability and safety of the mould in the production of medical plastic products.
High-precision processing: the mould adopts advanced CNC processing technology, with precision control at micron level, ensuring the accurate dimensions of various parts of disposable plastic syringes, such as piston, barrel, needle cap, etc., to meet the high standard requirements of medical equipment.
Aseptic Packaging Compatible Design: The mould design gives full consideration to the aseptic packaging requirements of the syringes, ensuring that the finished products are easy to automate the packaging, reducing the risk of secondary contamination, and meeting the strict hygiene standards of the hospital and clinical use environment.
Multi-cavity mould structure: optional multi-cavity mould structure, greatly improving production efficiency, suitable for large-scale mass production of disposable plastic syringes, reducing the cost of a single piece.
Material compatibility: Suitable for a wide range of medical grade plastics, such as polypropylene (PP), polyethylene (PE), etc., to ensure the transparency, rigidity and chemical stability of the syringe, in line with the material safety standards for medical devices.
Precision Cooling System: Built-in optimised cooling water channel ensures rapid cooling of the mould, shortening the production cycle and increasing productivity, while maintaining the dimensional stability of the syringe components.
Applicable Scenarios
Medical institutions: suitable for disposable medical supplies in hospitals, clinics, first aid centres and other places.
Vaccination: Suitable for large-scale vaccination programmes to ensure the safe, sterile and disposable use of syringes.
Laboratory research: to meet the demand for high-precision, sterile syringes in scientific research experiments.
In the field of modern medical device manufacturing, injection moulds for medical products play a crucial role. They not only ensure the accuracy and reliability of medical products, but also greatly enhance production efficiency and cost-effectiveness. From design to production, full-cycle quality control of medical product injection moulds is the key to achieving high quality in medical devices. In this article, we will discuss this process in depth, revealing how strict quality management measures can ensure that medical injection moulds are always in optimal condition.
Initial stage: design and planning
It all starts with design. The design of a medical injection mould must take into account the functional requirements of the product, the material properties and the production process. The design team uses advanced CAD software for 3D modelling to ensure that every detail of the mould accurately reflects the geometric characteristics of the product. In addition, the cooling system, gate locations, and venting slots of the mould are also evaluated during the design stage to ensure uniform filling and rapid cooling of the plastic melt during the injection process, and to avoid defects such as air bubbles and shrinkage holes.
Intermediate stage: mould manufacturing and validation
Mould manufacturing is a complex process involving high-precision machining technologies, such as CNC milling, electric discharge machining (EDM), wire-cutting, and so on. Manufacturers need to select high-quality mould steel to ensure that the moulds have sufficient hardness, wear resistance and corrosion resistance to cope with the high temperature and high pressure impact of the plastic melt during long-term production. After the moulds are manufactured, a series of tests, including trial moulds, are carried out to verify the performance of the moulds and the quality of the products formed. Quality control at this stage focuses on ensuring the dimensional accuracy and surface finish of the mould, as well as the geometric accuracy and appearance quality of the product.
Final Phase: Production and Continuous Monitoring
When the mould enters the production stage, the importance of full-cycle quality control becomes even more apparent. The production line is equipped with a variety of automated inspection equipment, such as optical measuring instruments and X-ray inspection systems, to monitor the dimensions and internal structure of the product in real time and to ensure that each component meets stringent standards. In addition, the parameters of the production process, such as injection pressure, temperature, cycle time, etc., also need to be precisely regulated to maintain the stability and consistency of product quality.
Continuous improvement and feedback loop
Quality control is not a one-time task, but a continuous process throughout the entire production cycle. Manufacturers of medical product injection moulds need to establish a comprehensive feedback mechanism to regularly collect production data, analyse the wear and tear of the moulds and the failure rate of the products, make timely adjustments to the process parameters, and even carry out the necessary maintenance and repair of the moulds. This attitude of continuous improvement will help to extend the service life of the moulds and reduce production waste, while continuously improving the quality of medical products.
Conclusion
Full-cycle quality control of injection moulds for medical products is a reflection of the pursuit of excellence in the medical device manufacturing industry. From the innovation of design, to the fine manufacturing, to the high efficiency of production, each link is inseparable from strict quality management. Only in this way can we ensure that medical products are safe and reliable in clinical applications and bring real health benefits to patients. With the continuous progress of medical science and technology, the manufacturing process and quality control strategy of medical product injection moulds will usher in more innovations and challenges in the future, and make a greater contribution to the cause of human health.